Die Casting in Malaysia: A Growing Hub for Precision Manufacturing
BusinessDie casting is now an integral component of the manufacturing industry in Malaysia which plays an essential function in the manufacture of top-quality metal components for various sectors. The process of manufacturing is advanced and involves injecting molten metal into a mold at high pressure, allowing for the production of accurate and robust parts, with no finishing work required. Over the years, Malaysia has emerged as the leading player in die casting, attracting both local and international companies searching for cost-effective and reliable production options. Thanks to its location in the middle of Asia as well as a highly developed infrastructure and highly skilled workers, Malaysia continues to strengthen its status as a top center for manufacturing die casting. The country’s ability to meet the growing global demand for precision-engineered components has led to it becoming a top choice for industries seeking high-end metal casting solutions.
Technological advancements in Malaysia’s die casting industry have significantly contributed to its growth and efficiency. A lot of manufacturers are embracing automated manufacturing and Computer-aided Design (CAD) systems to enhance precision and efficiency in the production process. Robotics and artificial intelligence are also implemented into production facilities which reduce human errors and improving productivity overall. In addition, businesses invest in environmentally friendly methods of casting like recycling materials and energy-efficient processes to lessen the environmental impact. The innovations do not just improve product quality but also align with global standards, making Malaysian companies in die casting much more appealing to international customers. By pursuing continuous advancement and research, Malaysia is set to remain at the forefront of the technology used in die casting over the years ahead.
One of the primary industries benefiting from Malaysia’s die casting capabilities is the automotive sector. Automotive companies rely on die-cast aluminum as well as zinc components for producing lightweight but durable vehicle components. Die-casting engine blocks, transmission housings and other structural components contribute to vehicle effectiveness and efficiency in fuel and are therefore essential for the modern manufacturing of cars. As electric vehicles are becoming more popular, the shift to (EVs) have further boosted the requirement for high-end die-cast components, since automakers are looking for lightweight components to improve the efficiency of batteries and also reduce overall vehicle weight. Malaysian die-casting firms have adapted to these changes through upgrading their facilities, and adopting advanced casting techniques to meet requirements of an ever-changing automobile business.
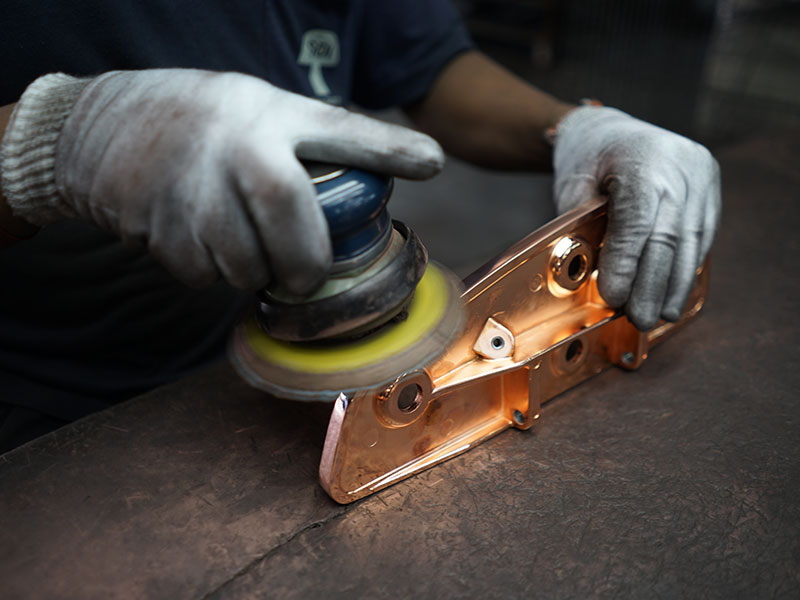
Apart from the automotive sector, Malaysia’s casting industry also plays an important part in electronic and consumer goods industries. Electronics requires high-end, precision-engineered die-cast parts for many apps, like laptops, smartphones and home appliances. They provide structural stability while maintaining a lightweight and compact design, essential for modern electronic devices. Malaysia’s role as a key electronics manufacturing hub has led to a high demand for die-cast components and is driving the growth of the field. In addition, manufacturers of consumer goods benefit from die casting in producing high-quality metal parts for household products, kitchenware and power tools. Die casting’s versatility allows for the production of complex and robust components that increase the product’s quality as well as functionality. For more information please Continue Reading
Despite the promising growth of Malaysia’s die casting industry there are numerous issues which require strategic approaches. The fluctuating costs of the raw materials used, including zinc, aluminum, as well as magnesium, could influence production costs as well as profit margins. In addition there is competitors from other manufacturers like China and India is putting the pressure on Malaysian companies to keep their market share. To remain competitive, firms must focus on innovation, quality assurance, and customer support, making sure that their products meet global industry standards. Government support through grants for research and development and workforce development programs as well as tax incentives, can aid in strengthening the industry. If these issues are addressed in a proactive manner, Malaysia can continue to grow its die casting industry and also attract investment from foreign manufacturers.
Die casting’s future in Malaysia looks promising, driven by the technological advances and increasing demand for precision-engineered components. The use of Industry 4.0 technologies, including machine learning, data analytics and monitoring using IoT, is expected to enhance the efficiency of production and reduce costs. Sustainability will also be a important consideration, with companies adopting eco-friendly practices to align with international environmental standards. While Malaysia is continuing to establish itself as a leader in manufacturing precision and die casting, the industry plays a key function in the supply of high-quality components to a wide range of industries worldwide. Through a commitment to quality and innovation, Malaysia is set to continue to be an influential force within the worldwide die casting industry for a long time to in the future.